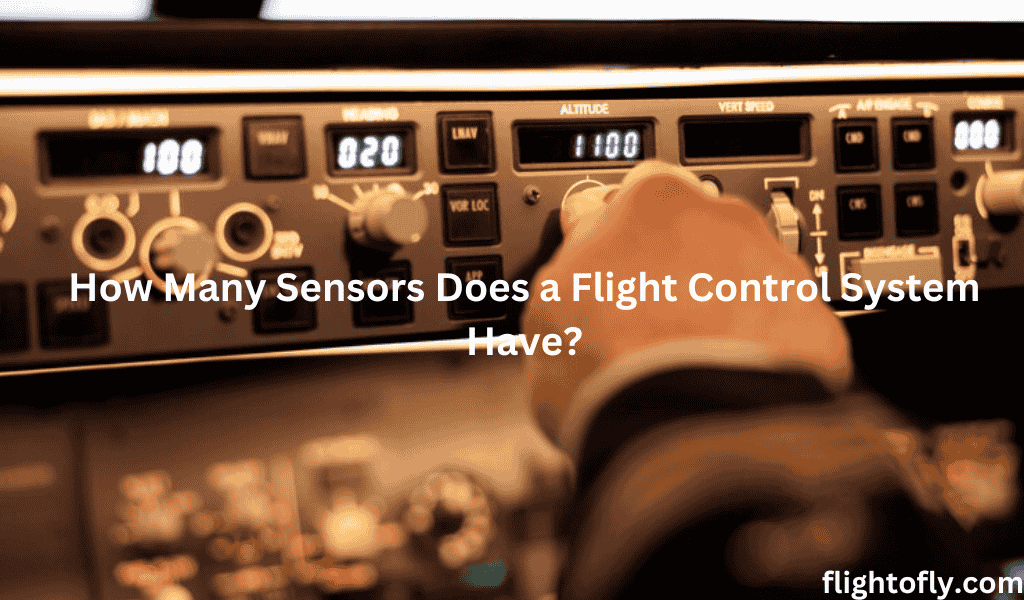
How Many Sensors Does a Flight Control System Have?
Modern flight control systems use anywhere from 20 to over 100 sensors, depending on the aircraft’s size and complexity. These sensors work together to monitor and manage everything from altitude and speed to engine performance and stability. Without them, flying would be far less safe and efficient. Let’s discuss the different types of sensors, their functions, and why they are crucial for every flight.
Flight control systems are crucial for aviation, managing an aircraft’s direction, altitude, and speed to ensure stability and safety. They rely on a network of sensors that monitor position, pressure, acceleration, and temperature, providing real-time data for smooth operations and passenger safety.
Check: Can You Be a Flight Attendant with a Felony?
What is a Flight Control System?
A flight control system is responsible for managing an aircraft’s movement, including direction, speed, and altitude. It consists of mechanical components, electrical systems, and software that work together to ensure safe operation.
In modern aircraft, flight control systems rely on fly-by-wire technology, where electrical signals replace mechanical controls. Sensors form the backbone of these systems, feeding crucial data to the onboard computer for decision-making.
Types of Sensors in a Flight Control System
Flight control systems use multiple types of sensors, each with a specific role. Let’s break down these sensors and their functions.
1. Position Sensors
The Position sensors track the location of various control surfaces, including:
- Rudder: Controls the aircraft’s side-to-side movement (yaw).
- Elevators: Adjust the nose up or down (pitch).
- Ailerons: Help with rolling movements.
Position sensors ensure these surfaces respond accurately to pilot commands or autopilot inputs.
2. Inertial Sensors
Inertial sensors include gyroscopes and accelerometers, which measure:
- Rotation: It Helps to maintain stability during turns or turbulence.
- Acceleration: Detects changes in speed and direction.
These sensors are essential for determining an aircraft’s orientation and ensuring smooth flight paths.
3. Pressure Sensors
Pressure sensors are critical for measuring altitude and airspeed. They fall into two main categories:
- Barometric Pressure Sensors: They determine altitude by analyzing air pressure changes.
- Differential Pressure Sensors: They measure airspeed by comparing pressure differences.
These sensors work together to keep the aircraft at safe altitudes and speeds.
4. Angle of Attack (AoA) Sensors
The angle of attack sensors monitors the angle between the oncoming airflow and the wing. This data is vital for:
- Preventing stalls.
- They ensure optimal lift during takeoff and landing.
AoA sensors play a key role in maintaining aerodynamic efficiency.
5. Temperature Sensors
Temperature sensors monitor various systems, including:
- Engine Temperatures: They prevent overheating or damage.
- Environmental Temperatures: It helps to manage anti-icing systems.
By monitoring temperature, these sensors enhance safety and performance in different weather conditions.
6. Proximity Sensors
Proximity sensors detect the position of landing gear, flaps, and other movable components. For instance:
- They confirm whether landing gear is fully deployed before touchdown.
- They ensure flaps are positioned correctly during takeoff and landing.
7. Load Sensors
Load sensors measure the stress on an aircraft’s wings and landing gear. They provide data to ensure the plane doesn’t exceed its structural limits during turbulence or heavy landings.
Types of Sensors and Their Specifications
Sensor Type | Function | Specifications |
Position Sensors | Detect the position of control surfaces like rudders, ailerons, and elevators. | – Accuracy: High precision (< 0.1° deviation)- Response Time: < 10 ms- Type: Rotary or linear potentiometers |
Inertial Sensors | Measure acceleration, rotation, and tilt to maintain stability. | – Type: Gyroscopes and accelerometers- Accuracy: ±0.01°/s (gyroscopes)- Data Rate: Up to 1,000 Hz |
Pressure Sensors | Measure airspeed and altitude by analyzing pressure differences. | – Type: Barometric and differential sensors- Range: Up to 100,000 ft altitude- Accuracy: ±0.01% FS |
Angle of Attack Sensors | Monitor the angle between the wing and oncoming airflow to prevent stalls. | – Range: -20° to +40°- Accuracy: ±0.5°- Response Time: < 20 ms |
Temperature Sensors | Measure engine and environmental temperatures to ensure optimal performance. | – Type: Thermocouples or RTDs (Resistance Temperature Detectors)- Range: -60°C to +1,200°C- Accuracy: ±1°C |
Proximity Sensors | Detect the position of landing gear, flaps, and other movable components. | – Type: Inductive or capacitive sensors- Detection Range: Up to 50 mm- Response Time: < 1 ms |
Load Sensors | Monitor stress on wings, landing gear, and other structural components. | – Type: Strain gauges or piezoelectric sensors- Range: Up to 200% of rated load- Accuracy: ±0.1% |
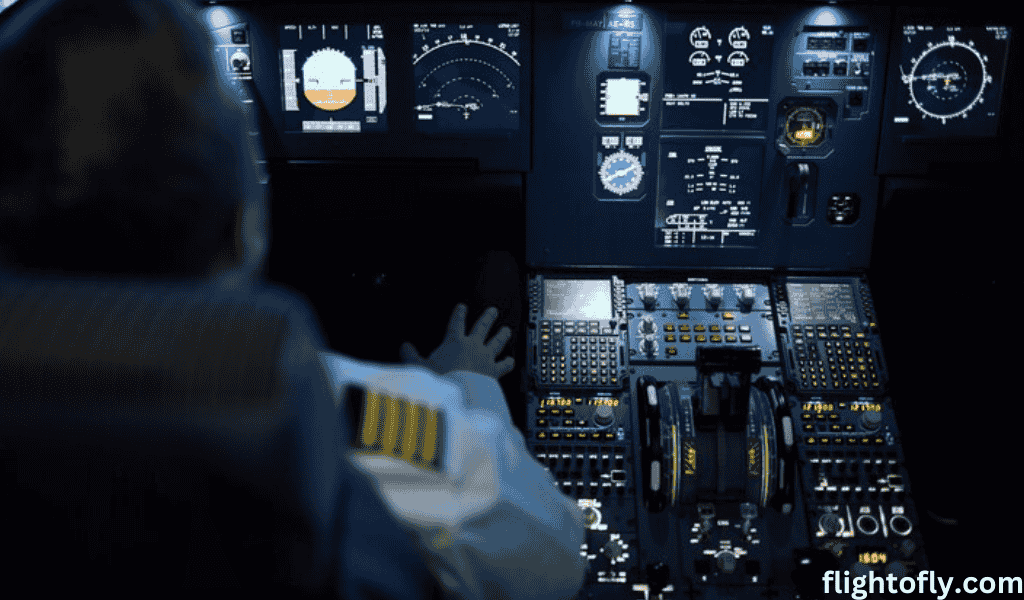
How Many Sensors Are in a Flight Control System?
The exact number of sensors in a flight control system varies depending on the type and complexity of the aircraft.
- Smaller Aircraft
For smaller planes, such as private or regional aircraft, flight control systems may include 20 to 50 sensors. These aircraft have simpler systems that require fewer sensors to monitor basic operations.
- Commercial Jets
Large commercial airplanes, like the Boeing 737 or Airbus A320, use more advanced systems with 50 to 100 sensors. These include additional sensors for redundancy and enhanced monitoring.
- Modern Long-Haul Jets
Modern jets, such as the Boeing 787 or Airbus A350, can integrate over 100 sensors in their flight control systems. These aircraft use state-of-the-art technologies to optimize fuel efficiency, ensure passenger comfort, and enhance safety.
The Role of Redundancy in Sensor Systems
Aircraft sensors often come with built-in redundancy. This means multiple sensors perform the same function. Why is this important?
- Reliability: If one sensor fails, others can take over.
- Safety: Redundancy ensures continuous operation in critical areas, such as altitude and airspeed monitoring.
- Accuracy: Comparing data from multiple sensors helps detect and correct errors.
For instance, a commercial jet may have three angle-of-attack sensors instead of just one. This ensures consistent and accurate data, even if one sensor provides faulty readings.
Why Are Sensors Crucial in Flight Control Systems?
Sensors are vital for the safe and efficient operation of aircraft. Here’s why:
1. Real-Time Data Collection
Sensors collect real-time data about the aircraft’s performance, surroundings, and internal systems. This information allows pilots and autopilot systems to make quick, informed decisions.
2. Automation
Modern flight control systems rely heavily on automation. Sensors feed data to the autopilot, enabling it to handle tasks like maintaining altitude, adjusting speed, and even landing in low visibility.
3. Safety Enhancements
Sensors help detect potential issues before they escalate. For example:
- The angle of attack sensors prevents stalls.
- Temperature sensors alert pilots to overheating engines.
4. Fuel Efficiency
By providing precise data, sensors enable better fuel management. This reduces costs and minimizes the environmental impact of aviation.
The Evolution of Flight Control Systems
Flight control systems have come a long way. Early airplanes used mechanical controls that relied on the pilot’s physical effort. Modern systems are highly automated, with computers processing data from hundreds of sensors.
This evolution has led to:
- Safer Flights: Reduced human error through automated systems.
- More Efficient Aircraft: Advanced systems that optimize fuel and performance.
- Enhanced Passenger Comfort: Smoother flights with fewer disruptions.
Challenges in Sensor Technology
Despite their importance, sensors face several challenges:
- Environmental Factors: Extreme temperatures, turbulence, and moisture can affect sensor performance.
- Maintenance: Sensors require regular calibration and testing to ensure accuracy.
- Cost: High-quality sensors add to the overall cost of the aircraft.
To address these challenges, manufacturers continually develop more durable, efficient, and cost-effective sensor technologies.
How Pilots Use Sensor Data
Pilots rely heavily on sensor data during every stage of flight. Here’s how:
- Takeoff and Landing: Sensors provide critical information about speed, altitude, and weather conditions.
- Mid-Flight: Data helps maintain stability, avoid turbulence, and optimize fuel use.
- Emergency Situations: Sensors alert pilots to potential issues, enabling quick action.
Conclusion
Flight control systems depend on many sensors to ensure safe and efficient flights. Each plays a crucial role, from position sensors to pressure, temperature, and angle-of-attack sensors. The number of sensors in a flight control system varies based on the aircraft type, with modern jets often using over 100 sensors for optimal performance.
As aviation technology advances, sensors will evolve, making air travel even safer and more reliable. Their role in modern flight control systems cannot be overstated, they are the eyes and ears of every aircraft.